The craft of beer and the art of coding
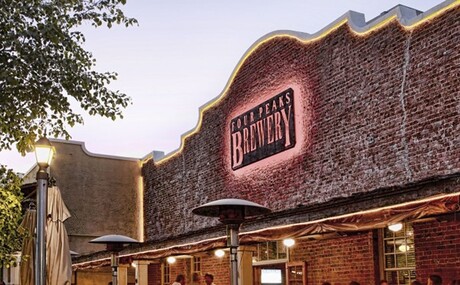
Production downtime and unforeseen costs due to faulty marking systems posed significant challenges for one of Arizona’s largest craft breweries, Four Peaks. Frequent printhead clogs impacted production efficiency, but now this has been solved using LEIBINGER’s printing technology with patented nozzle seal technology.
Over the last century, the red-brick building at 1340 8th Street, Tempe, Arizona has had many uses. It has been an ice factory, a creamery and even a recording studio before finding its current role as home to Four Peaks craft beer. Founded in 1996, Four Peaks beer brands include Kilt Lifter and Wow Wheat, and it was acquired in 2016 by American brewing company Anheuser Busch.
To enjoy craft beer at its best, you need to drink it fresh; therefore, expiration dates are printed on every can or bottle at the brewery. This helps to ensure quality product for consumers, but in the past it created a headache for Gary Fogg, who has been Head of Production at Four Peaks since 2018.
Before the LEIBINGER machines were installed, quality issues would often arise as the print heads on the other manufacturer’s printers became clogged. Every 15 minutes, the legibility of the print would be checked. If the expiration date was not perfectly clear, the production line would have to stop for up to an hour while the print head was cleaned.
Even worse, with 250 cans rolling off the line every minute, Fogg might find himself with almost 4000 misprinted beers. This would mean either unnecessary time and effort washing and re-printing — or the beer would be wasted. And this happened at least once a week, sometimes even every day.
With experience from a previous role on how to solve the issue, Fogg promptly replaced the printers with LEIBINGER printers when he first started this role with the company — the impact on productivity was instant. “When I first started we were doing cleanings every week at least — sometimes every day. Now we don’t even have to do it every month.”
There were other benefits apart from saving time. Cleaning print heads requires solvent, which can have a harmful impact on the environment. If the print head doesn’t need to be cleaned, you don’t need so much solvent — thus improving the environmental impact of the plant while also saving money.
There were also environmental advantages with the cartridges/bottles: “They’re designed to empty completely — so no hazardous waste. With other cartridges, I had to empty residual solvent and ink into a tank and have it pumped out every month by specialists for proper disposal. That takes time and money,” Fogg said.
Breweries can be busy, hot, humid places, which makes coding difficult for some printers — but not LEIBINGER: “I’ve seen LEIBINGER machines working perfectly in possibly the most difficult environment you could find, such as above the pasteurisation funnel where the air is damp, hot and dirty. But it still worked fine,” Fogg said.
Another problem arose with the condensation on the outside of pre-filled bottles. This meant that the soft-pigmented yellow ink which was being used was flaking off instead of sticking to the glass surface. Tim Robinson of RMH Systems, a coding machine specialist, suggested changing to a hard-pigmented silver, which adhered better. He said it was important that they were using LEIBINGER machines as he wouldn’t recommend this for all machines.
“Once you put a certain ink in there, some machines are not big on changing. You have to change the nozzles, the oscillators, and we would never recommend it. With LEIBINGER you can just flush it out and start again with a different ink,” Robinson said.
Four Peaks and LEIBINGER make good partners since both companies believe that success comes from quality, a point that Fogg summarises below:
“At the end of the day, our job is to brew great beer and get it out there to thirsty customers. And coding should be such a simple task. If it’s legible and repeatable and we don’t have downtime, that’s all we need. And that’s what we’ve had for years now with LEIBINGER.”
Klöckner Pentaplast kp Elite Nova MAP tray
Klöckner Pentaplast has launched the kp Elite Nova — a next-generation modified...
East Coast Canning + Printing BulletProof digitally printed can
After three years of development, New South Wales-based East Coast Canning + Printing (East...
Scan Wrap multi-purpose stretch wrapper
Scan Wrap is a multi-purpose stretch wrapper that wraps, weighs, sizes, records, transmits data...