Shelf-ready packing with speed and precision
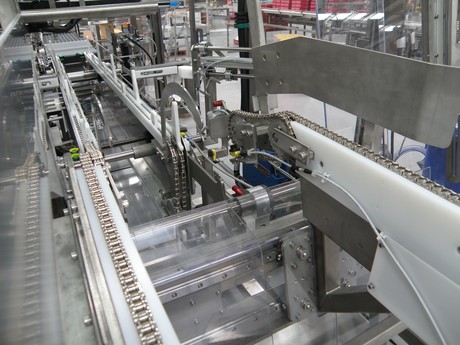
When a leading food manufacturer upgraded its condiment production line it needed an end-of-line solution to take the bottles and pack them into a configuration suitable for supermarket shelves.
Having all the products on the supermarket shelf neatly packed with labels facing forward used to be a labour-intensive task, but now, thanks to advances in technology, bottles can be positioned into cartons, forward facing as a fully automated process.
A global food manufacturer asked Hot Melt Packaging Systems (HMPS) to provide such an end-of-line solution for its high-speed condiment production line.
To meet growing demand, the manufacturer had previously upgraded its main condiment production line to produce twice as much product in half the time. Bottles are sterilised, filled, capped and labels applied. The production line produces different sized and shaped bottles ranging from 500 mL to 4 L. To accommodate this, there is a multiple range of case sizes, pack configurations and bottle shapes.
According to Warren Booker, NSW state manager at HMPS, “In Australia, manufacturers are challenged by having to produce so many different products in the one machine. In countries with larger populations, like the US and Europe, one machine can be dedicated to a specific product, which makes the machine design more simplistic. The Australian market has a unique requirement where they need a machine to be flexible to grow with the business and pack a range of different products in different packing arrangements.”
HMPS worked closely with the customer to design a fully automated system that meets all the requirements for this application today but also has the flexibility to meet future demands.
The challenge ahead was to pack bottles that are coming off the production line at 100 bottles/min into a six by three pack configuration with labels forward facing. “There were fundamental considerations that required attention in the design phase to achieve this with a key focus on detailed simulation to make sure the advanced level of motion control required could be achieved,” explained Booker.
Given the large range of products being produced and the need for shelf-ready cartons, this production line had clear and precise requirements which HMPS had to comply with. Using the latest technology and working closely with the customer-specified needs has allowed this project to be a smooth transition into full production speed maintaining high efficiency and reliability.
Having worked on previous projects with Rockwell Automation, HMPS knew that the Integrated Architecture system would provide the best solution for this application. Allen-Bradley CompactLogix uses a common control engine and integrates safety, motion, discrete and drive capabilities in the case packer system.
Advanced motion control is provided by Allen-Bradley Kinetix 5500 Servo Drives and PowerFlex variable speed drives. Given the high-speed packing requirements of the system, safety door switches and guarding was provided by Allen-Bradley industrial components.
In addition, the case packer system has integrated control, drives and safety capabilities via Ethernet using Stratix 5700 Ethernet switches. PanelView Plus 7 provides high-quality HMI for the system. “The Rockwell Automation solution provides a completely integrated and reliable system for the case packer and also provides the framework for a smart machine for HMPS to leverage the Connected Enterprise,” said Michael Vlahos, OEM sales manager at Rockwell Automation.
“To futureproof the machine, a degree of adjustment in the machine had to be considered. Due to the need for relatively quick changes, we have supplied a fully automated system,” commented Booker.
All the SKUs or product range are listed on the main screen so the operator can go to see the core product and the machine will automatically resize at a touch of a button. In this way, the machine can apply the resize down to just using the one operator. In addition, the machine won’t run until everything is in exactly the right position and all guards and doors are in the safe (closed) position.
“We have a modem in the machine that looks at running time and reliability factor. In this way we have a track record of parameters as part of the control system, how it’s been running, how long etc. We have the software which allows us to log in remotely,” added Booker.
Phone: 08 8150 1000
Emerson Energy Manager
The Emerson Energy Manager is a pre-engineered hardware and software solution designed to...
PIQET 5.0 sustainable packaging tool
Lifecycles has launched version 5.0 of its Packaging Impact Quick Evaluation Tool (PIQET).
Timmer D4 glue pump
The D4 glue pump is used for dosing of glue and adhesives, and is suitable for labelling of...