Sensor intelligence replaces mechanical singulation
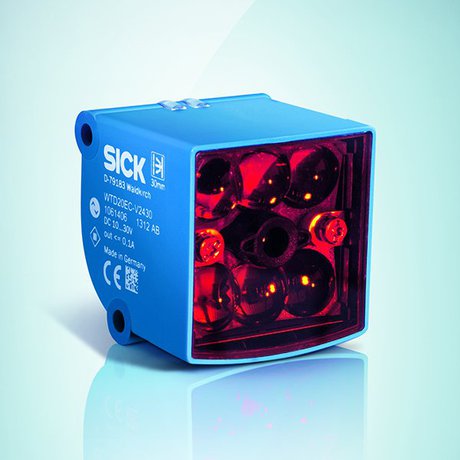
Fruit juice manufacturers offer a wide range of products — from the purest fruit juices and nectars, to native and exotic fruits and berries, right through to vegetable juices. In the production plant of a well-known fruit juice manufacturer, the fruit juices are pressed, decanted into a huge range of Tetra Pak cartons and then packaged again in trays without any interruptions. The DeltaPac MultiTask photoelectric sensor from SICK is responsible for this last task.
A vast product range requires a varied selection of packaging shapes and sizes in all key beverage units. To be able to manage all internal and external flows of goods in large quantities and at high speed, the products need to be packaged reliably. The different Tetra Pak cartons filled with juice are therefore packaged again in trays. A tray is a box which is usually open and made of corrugated cardboard. Each tray holds either six or 12 fruit juice cartons. The fruit juice cartons are conveyed along a line before being placed in the trays. The juice cartons must be counted and must reach the downstream secondary packaging lines intact so that the right number of cartons ends up in the corresponding tray.
Gaps cost time and money
Previously, a mechanical singulation process was used to determine the right quantity of juice cartons. This left gaps on the belt to enable the juice cartons to be counted. As a result, the photoelectric sensors used at the time could detect the edges of the packaging and count the cartons. To create the gaps, a belt brake was used to accelerate the juice packages, which were moving comparably slowly. This often resulted in faults on the packaging line and damage such as squashed juice cartons. It was also possible that, if a gap was not created properly, it would not be detected by the photoelectric sensor and some cartons would not be counted at all. This solution was not just highly prone to errors, it also meant that the machine required constant maintenance. The belt needed to be lubricated as effectively as possible so that the juice packages were able to slide. Added to this, the belts had to be readjusted over and over again due to the different packaging formats. In the event of machine downtime, searching for the cause of the problem was incredibly time-consuming, creating a new problem in itself.
The problem with too much colour
The old packaging system fitted with conventional optical sensors could not cope with the fruit juice manufacturer’s wide range of packaging. It was not just the different formats of the juice packages, but rather their colourful design that proved to be too much for the photoelectric retroreflective sensors, which work with reflected light. When detecting very dark, extremely bright, shiny or highly colourful surfaces, the light was only reflected partially, too much or not at all, causing false signals. This resulted in the juice cartons being counted incorrectly, which could cause crashes in the bottleneck and incorrect quantities in the trays. On top of all this, the manufacturer still had to carry out a weight check at the end of the line using scales.
Fusing technologies to enable continuous detection
meurer Verpackungssysteme, a leading manufacturer of packaging machines, has developed a solution with SICK which makes it possible to dispense with the complex mechanical singulation process when counting juice cartons. In the fully automatic CM/TP-B tray packer from meurer, the DeltaPac MultiTask photoelectric sensor from SICK has taken on this task. The sensor detects and counts the juice cartons — which are lined up on the packaging line — without any gaps, even before the cartons are separated onto the downstream secondary packaging lines, where they are placed in six-pack or 12-pack trays.
Creating a gap is not necessary now, as the MultiTask photoelectric sensor combines two intelligent technologies. The patented Delta-S-Technology developed by SICK consists of four Pin-Point 2.0 LEDs and two high-resolution energy scales, each with two receiving elements. The four receivers on the two energy scales receive the same amount of light, while the light beams from the four PinPoint 2.0 LEDs detect the leading side of the juice cartons. At this point, the light energy is balanced. However, as soon as the leading edge of a juice package is brought into the beam of light, the amount of light energy is distributed to the receivers in varying degrees, disrupting the balance.
Depending on the packaging contour, a distinct energy signal is created and the sensor detects where the reflected light is coming from and sends a corresponding switch signal. The DeltaPac sensor combines Delta-S-Technology with the innovative SIRIC ASIC technology from SICK and distance measurement for background suppression. The detection process, which is based on this fusion of technologies, works completely independently of the colour, format or surface structure of the juice carton. In addition, interfering factors such as glare from windows or changes in contrast do not impair the detection reliability of the intelligent sensor in any way. The result: the correct number of juice cartons ends up in the downstream tray packaging lines.
Higher efficiency and quality in the packaging process
The tray packer from meurer, complete with integrated SICK sensor intelligence, makes processing the widest range of packaging colours and formats incredibly simple. With the software and PLC supplied by meurer, the packaging speed and formats can be specified and the DeltaPac sensor will adjust itself accordingly. Time-consuming maintenance and adjustment work is no longer required, thanks to the high level of detection reliability and the fact that the juice packages are constantly on the move during the counting and separation process. Furthermore, machine downtime is significantly reduced and it is no longer necessary to weigh the trays at the end of the line.
Phone: 1800 334 802
Henkel Loctite Liofol LA 7837/LA 6265 solvent-free adhesive system for packaging
The system is tailored for applications involving high thermal stresses — in particular...
Klöckner Pentaplast kp Elite Nova MAP tray
Klöckner Pentaplast has launched the kp Elite Nova — a next-generation modified...
East Coast Canning + Printing BulletProof digitally printed can
After three years of development, New South Wales-based East Coast Canning + Printing (East...