Optimising a returnable Coca-Cola bottle system
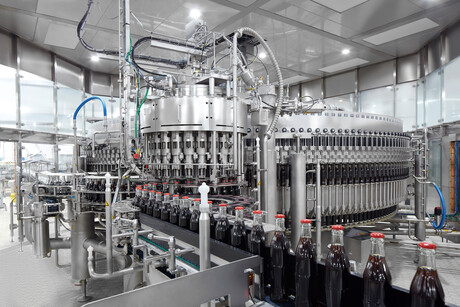
A Coca-Cola plant in Mannheim, Germany, has installed a returnable glass bottle line from KHS to boost its recycling abilities. The automated line takes bottles, cleans and rinses them, and then sorts them out to be reused. The system fills six bottle formats: four in 200 mL and two in 330 mL sizes, with different use cases for the different sizes.
“The smaller sizes are primarily destined for the hospitality trade, where the packaging has to be a bit more impressive than for retail,” said the plant manager, Christopher Bee. “This is why the Coca-Cola, Fanta, Sprite and mezzo mix brands on this line have their own respective bottle designs. We process two formats for the bigger containers that are also sold in the retail trade: what’s known as the contour bottle for products in the Coca-Cola family and our green multibottle for Fanta, Sprite and mezzo mix.”
The sorting and washing are all done automatically and there is no need for the cleaned bottles to be sent to a warehouse before being refilled. Instead they are sent right off to the filling line.
The system has only one manual element: prior to being sorted, crates of empty bottles are scanned by the sorting system and it is here where any obstacles like paper cups or film must be removed by hand. Otherwise the system operates in a wholly autonomous manner.
“The smaller bottles are set down on a different conveyor where they’re separated and guided to different lanes with the help of camera systems and pushers,” Bee said. “Here, we aim to manipulate the containers as little as possible: in other words, to ensure that they have very little contact with the machine. In this way, we can keep the risk of something falling over at such high speed to a minimum.”
The line’s bottle washer saves around 40% on energy and water usage compared to previous generation systems. Energy is saved elsewhere too, with its carriers having a reduced weight and more carefully placed openings to make rinsing bottles easier and more efficient. Finally, the spraying system uses less pressure during downtime and thus reduces electricity consumption by up to 80%.
The plant is now operational and processes 60,000 bottles an hour.
Phone: 03 9335 1211
Koor refillable bottle
Koor has designed an easy-to-refill packaging solution as an alternative to single-use food pouches.
Ravenwood Packaging Nobac 40B Bottle Labeller
Ravenwood Packaging has launched the Nobac 40B Bottle Labeller, an entry-level linerless bottle...
Ravenwood Nobac 40B Linerless Bottle Labelling Machine
The Nobac 40 linerless applicator is designed to provide a sustainable and cost-effective...