Clean and safe: the real packaging challenge
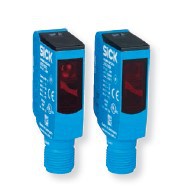
The L29 single-beam photoelectric safety switch, developed for the packaging manufacturer MULTIVAC, stops dangerous movements safely if someone reaches into the forming station in a thermoforming packaging machine. Together with MULTIVAC, SICK has developed custom solutions such as inductive proximity sensors, fork sensors, photoelectric retroreflective sensors for transparent objects, encoders and more for packaging machines used in the food industry.
MULTIVAC is one of the leading global suppliers of packaging solutions. Alongside thermoforming packaging machines, the portfolio covers everything from tray sealers, vacuum chamber machines, chamber conveyor belt machines, labellers, quality control systems and automation solutions right up to turnkey lines. With around 4500 employees and more than 70 subsidiaries, the company develops and builds turnkey packaging lines which supply, manage, separate, inspect and label packaged products and their secondary packaging. The processes of a packaging line can be controlled centrally via the HMI 2.0 user interface from MULTIVAC, making it possible to monitor process data and process it further electronically, so that products are traceable.
Everyone is looking for the ideal solution
The forming station in a thermoforming packaging machine creates packing moulds. The machine uses heat to warp the foil and compressed air and a vacuum to thermoform it. It is then transported to the infeed area where the moulds are filled with the products. This is all done with mechanical movements. This means that the transition from the forming station to the infeed area must be secured in such a way that the machine movement stops as soon as a person enters the area.
As part of the redevelopment of its safety concept, MULTIVAC was on the lookout for a photoelectric switch that fulfilled the new requirements as effectively as possible. Ideally, the photoelectric safety switch should have an evaluation unit. However, the conventional single-beam photoelectric safety switches from SICK were too big. SICK therefore developed a photoelectric safety switch from one of the photoelectric switches used for detection in automation technology.
SICK’s L29 single-beam photoelectric safety switch slots seamlessly into the HMI 2.0 user interface from MULTIVAC. The sender axes can be retained as the photoelectric switch can be fitted in the same position as the previous photoelectric switches, due to its compact size. The L29 has enclosure ratings IP67 and IP69K, as well as Ecolab approval. The VISTAL housing gives the product outstanding mechanical ruggedness. In addition, the housing had to be adapted to the MULTIVAC design and the logo and part number from MULTIVAC had to be visible on the sensors. SICK met all of these requirements.
Making safety a priority
The L29 photoelectric switch fulfils the requirements of safety classes type 2 (IEC 61496), SIL1 (IEC 61508), PL c (EN ISO 13849) when combined with a test device from the Flexi Classic product family (UE410-MU). As far as electromagnetic compatibility is concerned, stricter threshold values are required. The L29 can achieve these values with some small adjustments to the electronics. For safety reasons, the maximum permitted aperture angle must be observed. If the angle is too large, the sensor cannot detect hands or fingers due to the reflective surface. This is where the L29’s PinPoint LED with its highly visible light spot comes into play. The SIRIC optical technology makes this photoelectric switch more powerful than conventional ones. It is not sensitive to any known optical and high-frequency influences such as ambient light, vibrations or electromagnetic influences.
Strong housing
The L29’s VISTAL was one of the key motivating factors behind MULTIVAC’s decision to opt for the product. VISTAL is a rugged housing material, consisting of high-strength plastic reinforced with glass fibre. With mechanical properties which exceed those of conventional plastics, the stable and rigid sensor housing is resistant to chemicals, meaning that cleaning agents pose no problem for the sensor. This is essential in hygienic environments in the food sector, where MULTIVAC packaging machines are used. As MULTIVAC did not want the photoelectric safety switch to interfere with the safety concept of the machine, it was also adapted to match the design of the packaging machines. The TÜV, a German certification body, has issued the type test certificate, meaning that all safety requirements had been fulfilled.
Phone: 1800 334 802
BMT Blowscan and Thermoscan rPET bottle perfecting systems
Blowscan and Thermoscan are designed to help manufacturers improve PET bottle performance, reduce...
Henkel Loctite Liofol LA 7837/LA 6265 solvent-free adhesive system for packaging
The system is tailored for applications involving high thermal stresses — in particular...
Klöckner Pentaplast kp Elite Nova MAP tray
Klöckner Pentaplast has launched the kp Elite Nova — a next-generation modified...