How intelligent vision-based sorting and tracking benefits your organisation today
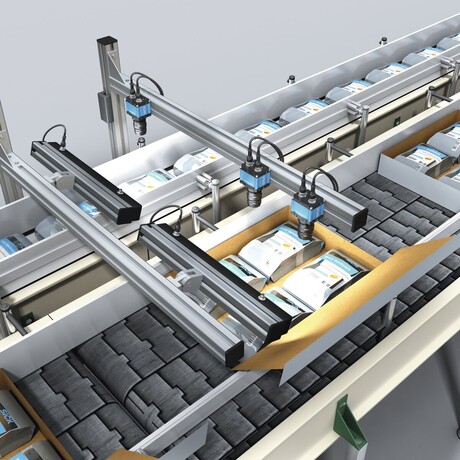
Tracking and managing the flow of packages efficiently relies on information. Not just static data represented by a barcode, but increasingly, all types of information relative to how goods are routed, sorted, processed, and shipped in distribution centres, factories and other facilities. The velocity and small-item packaging involved with e-commerce heightens this need for more information — including digital images — about read/scan events, label and package conditions, and package characteristics so that operations can run optimally.
If you can digitise information vital to material handling, leveraging image-based readers and other intelligent sensors, and tap into online archiving of images and read events, you can route goods in a better way during operations, and perform analysis to prevent misreads or low utilisation of equipment. The digitised information can reveal issues with package condition, label quality, or spacing/gaps issues on automated lines.
With online storage of images, an organisation can apply analytics to continually improve on read rates and have a handy archive to “prove” package condition. Here are a few key areas that are ripe for improvement with intelligent sensors and image-based readers:
- Lower than expected read rates in critical areas of a warehouse, leading to costly exception handling, shortages in downstream pick/pack areas, or incorrect orders. Image-based readers can address this challenge by capturing images that show the full range of package, label presentation, and label characteristics that impact read rates. Bad labels, packages that are too close together or too far from the read zone, are problems that can be solved with image-based readers and associated analytics.
- Suboptimal utilisation of high-end sortation, conveyor, or other materials handling equipment. A combination of image-based readers, photo eyes and digital array sensors (sensors which sweep a beam of light to detect what’s passing by) can be used to precisely track the leading and trailing edges of hard to detect items such as polybags. Knowing the leading/trailing edge of bags, as well as tracking whether asset components like tilt trays are occupied with goods, helps keep loop sorters and other materials handling assets fully utilised.
- Inability to rapidly or accurately capture full product characteristics on the inbound/ receiving side. Because image-based readers and supporting technology such as dimensioning sensors can capture information such as dimensions, label quality, as well as bar code data, the operation is better able to route received goods to the proper area. If a supplier label is damaged, it’s better to know that right away, or if a package is too large to be conveyed, it’s better to route that package differently from the start. Image-based readers and dimensioning sensors, placed at key points near receiving, allow for smoother workflows.
- No way of being able to quickly prove the condition of packages which leave your facility. Image-based readers and archiving of images and read events are the foundation for being able to proveout package/shipment condition. Analytics software that can quickly call up read events by day, time, and location also help address this issue.
In summary, being able to digitise package characteristics and read events is the next evolution in smart materials handling and traceability. While traditional bar code readers still have a role, to keep increasingly automated fulfillment centers as productive as possible, image-based readers and smart sensors are becoming a must.
Smart readers and sensors that address needs such as dimensioning allow operations to stay on top of changes in product mix and packaging attributes, as well as keep pace with the level of order velocity and complexity being driven by e-commerce.
This digitisation of package and read event characteristics may sound difficult to achieve, but with SICK’s comprehensive services, the right solutions can be chosen, implemented, and maintained. SICK’s experts can help match the right readers and sensors to the application, and its services team can perform maintenance on an ongoing basis, as well as come in before crucial peak seasons to make sure the sensors will perform as expected.
Racking Up Results: How Jimba Lamb Got Its Inventory in Shape
How a homegrown inventory solution helped United Meat Co's Australian arm, Jimba Lamb, gain...
PE20 Palletising System by Optima Robotics
Amid labour shortages, increasing expenses, and safety worries, businesses of all sizes are...
Sweet Success: How Fishbowl helped Niche Bakers scale
As we settle into the new year, the NAB's recent research report reveals Australian SMEs have...