Tubular conveyors keep coffee processor moving
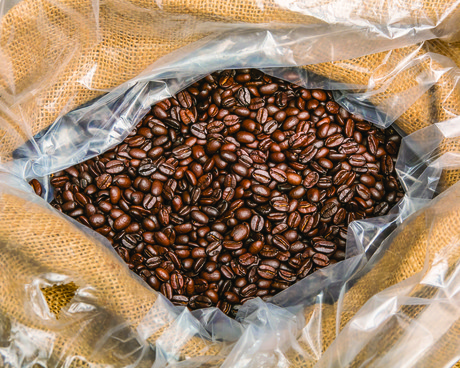
Porto Rico Importing Company has been doing business in New York since 1907, and today ships 1360 kg of coffee/day to its four retail stores, mail order customers and wholesale accounts.
At its Brooklyn roasting facility, Porto Rico roasts, blends, grinds and packages beans according to a strict schedule. At 465 m2, the facility is relatively small, so efficient material handling is critical to maintain production schedules, explained warehouse manager Mark Kasper.
To accomplish this, Porto Rico installed two tubular cable conveying systems, special hoppers, a portable flexible screw conveyor and a half-frame bulk bag discharger with an upper frame section that doubles as a filler, from Flexicon Corporation.
At the heart of the system are two FLEXI-DISC Tubular Cable Conveyor (TCC) circuits, which are able to move fragile coffee in all of its forms without degradation, dust or residual material in the conveyor at the end of a conveying cycle.
The conveyors transport coffee beans through 10 cm stainless steel tubes using low-friction polymer discs affixed to a stainless steel cable.
Immediately following discharge, the cable-disc assembly is turned 180° and passes an air knife for cleaning of any residual material, before travelling through the return circuit. At the intake end it is again turned 180°, before passing through a pick-up adapter where coffee is metered into the system.
Beans automatically feed from multi-bin hopper to blender
Porto Rico receives green beans in bulk bags that are unloaded from a discharge station and hopper, manually weighed and transferred in batches by a pneumatic conveyor into a roaster.
After roasting, beans gravity feed into a floor hopper where they are metered into the first tubular cable conveyor circuit, travelling 2.7 m horizontally, then 3.6 m vertically, and another 3.6 m horizontally to either a wall-mounted 368 L-capacity surge hopper for manual bag filling of non-blended batches or through two inline tubular discharge valves and two wye diverter valves into a special four-compartment hopper mounted on load cells in preparation for blending with other bean varieties.
“We need to convey the coffee quickly so we don’t slow down the blender,” explained Kasper.
Once the bean varieties have been delivered to the four-compartment hopper, a PLC weighs batches of up to four varieties, by selectively actuating the discharge valves beneath each compartment to deposit the desired amount of each bean into the blender, according to weight gain information transmitted by load cells underneath the hopper. Once the correct amounts are in place, blending begins.
Second TCC circuit from blender to grinder
The second TCC circuit, installed at a right angle to the first, transports blended beans from the hopper beneath the blender 1.8 m horizontally, then vertically 4 m and horizontally another 3.9 m where the beans are gravity fed through a hopper and a wye diverter valve. One leg is for filling 23 kg bags of whole bean blends and the other leg feeds the grinder.
From the grinder, a portable flexible screw conveyor, 3 m long, transfers ground coffee at a 45° angle into a bulk bag, secured in the upper section of the half-frame bulk bag discharger. The ground coffee degasses overnight in the packaging area. The next morning the bulk bag contents are discharged into a 113 L-capacity floor hopper within the split frame, from which a flexible screw conveyor transfers the coffee to a packaging machine for small wholesale packages.
Conveyors deliver undamaged product
The tubular cable conveyors replace a large pneumatic conveying system used in a previous warehouse. Kasper said the pneumatic conveyor was powerful and did a good job moving material. However, it broke a percentage of beans in the process, which detracted from product appearance.
The smooth operation of the lines requires minimal manpower for operations. Kasper said only two people work with him in the warehouse.
Phone: 07 3879 4180
Timmer quickLIFT and heavyLIFT vacuum hose lifters
Timmer has a range of vacuum hose lifters for safely lifting and lowering heavy goods.
Key Technology Iso-Flo, Impulse, Zephyr and Marathon vibratory conveyors
Key Technology introduces high-capacity vibratory conveyors for advanced food-handling applications.
Sidel RoboAccess_Pal S robotic and cobotic palletising solution
RoboAccess_Pal S, Sidel's latest robotic and cobotic palletising solution, will be in action...