Central palletising system for 28 packing lines of savoury products
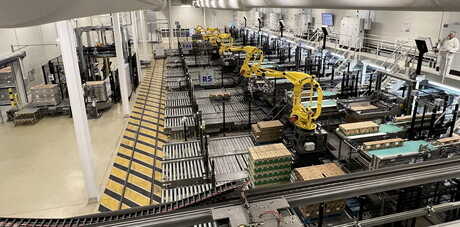
Sidel has delivered a central palletising system composed of eight robotic cells, connected to 28 packing lines at Unilever’s nutrition factory in Ploiesti, Romania, for savoury brands including Knorr.
Unilever’s dry nutrition portfolio at the factory includes meal makers, dish and sauce bases, and seasonings amongst others in various packaging formats — pouches, bags, cartons and multipacks. The different product lines also handle a large variety of secondary packaging options, including American boxes, tray and hood, tray and shrinking foil, and shelf-ready packaging.
With volumes tripling from 12,000 to 35,000 t per year, stockkeeping units rising from 200 to 1000 and packaging lines increasing from 14 to 28, Unilever was in need of a solution to futureproof the facility.
Sidel installed a centralised palletising system comprising eight robotic cells, several hundred metres of case and pallet conveyors, four pallet handling shuttles and two stretch wrappers, achieving a production rate of up to 98 pallets an hour. The consolidated system is connected to 28 packing lines.
The robotic cells are divided into two separate clusters — one with five robots and the other with three. Each cluster has one central pallet magazine for all pallet types and sizes, one induction shuttle for full pallet discharge and one compact shuttle for empty pallet delivery integrated underneath the robotic islands.
According to the capacity of each packing line and the palletising pattern requested, the cells have three or four product infeeds, ensuring a robot utilisation rate of 92%.
Designing the solution
Unilever’s plan was to keep the palletisation space in a separate area from the packing hall to easily accommodate the recurring packing line modifications. To connect the two areas, Sidel proposed a high-level conveying solution with spiral elevators to save space, facilitate circulation and increase the overall flexibility at the site.
Sidel was able to demonstrate its proposed arrangement using virtual reality glasses which allowed Unilever to visualise the full installation, check the space constraints and solve potential issues related to platforms, the operators’ access and the raw material flows. Speed simulations also helped to confirm the speed levels and the robot utilisation rate.
After the design phase, Sidel’s project management spanned from factory acceptance testing to site installation. All eight robot cells were completed in less than eight months. The modular concept accelerated installation as each cell was commissioned individually and at once integrated into the factory’s live packaging operations.
The energy-saving results
The central palletising system is integrated in the Unilever digital process. As soon as the operator selects the production order from the packing line, all the information related to the palletisation, including pallet size, type of pattern, number of rows/layers and the label to apply is all automatically set and transmitted to the corresponding palletising cell and the entire end-of-line set-up.
Unilever prioritises energy reduction with every project as the company is aiming to achieve a zero-carbon footprint by 2030.
“By using an energy-saving module for each robotic cell of this palletising installation from Sidel, we’re able to generate energy from the robotic arm deceleration and re-inject it into the network to be used by other robots or equipment within the line. Similarly, when a packing line is stopped for cleaning or changeover, conveyors enter standby mode as the photocells detect no products are being transported,” said Lucian Tarida, Process Engineer at Unilever.
Phone: 02 9899 4642
Hygiena e-commerce platform for food safety testing solutions
Hygiena has provided simplified access to environmental monitoring solutions through its...
EXAIR Model 7905 Digital Static Meter
EXAIR's upgraded Model 7905 Digital Static Meter can provide an essential first step in...
MTA TAE G air-cooled process chillers
TAE G air-cooled process chillers are specifically designed for use in the most demanding...